Powder, Foam, Liquid
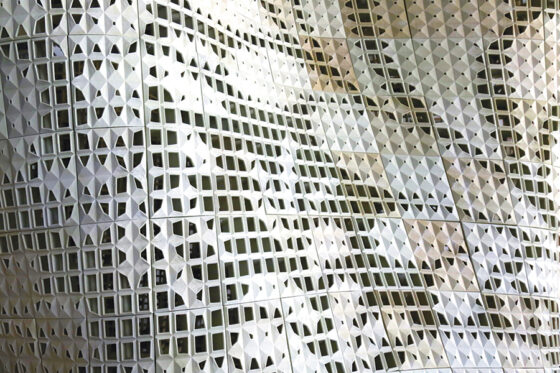
Powder, Foam, Liquid
Architect’s Newspaper
The latest experimentation with digital fabrication and alternative materials in 3D printing involves decomposing glass, sawdust, concrete, and even stone into baser forms such as powders and liquids. This diversifies the repertoire of materials that can be fed into a 3D printer. Associate Professor of Architecture Ron Rael’s recent project, Bloom, is a 3D printed, powdered concrete–based pavilion recently debuted at the Berkeley Circus.“The advantage of the powder-based process is that it accommodates a number of materials, any material that we can grind into powder,” said Ronald Rael. The environmental and economic implications of cost cutting, automation, and recycling in design, construction, and manufacturing are game-changing. The undulating, mesh-like structure consists of 16 concrete panels, each one light enough to be lifted into place by two people, rather than a crane. Rael mixed polymers with cement and fibers to produce resilient, lightweight, yet “high-resolution” concrete skeletons. “The extrusion-based processes involve pumping wet cement through a nozzle and you can only stack wet cement so high,” said Rael of traditional 3D printing. “But with a powder-based process, we could make [lightweight] blocks and send them to the moon.” Composed of 804 custom-patterned bricks, the mesh-like configuration increases load-bearing capacity while decreasing surface area