Forest to frame: Paul Mayencourt bridges forest management and sustainable construction
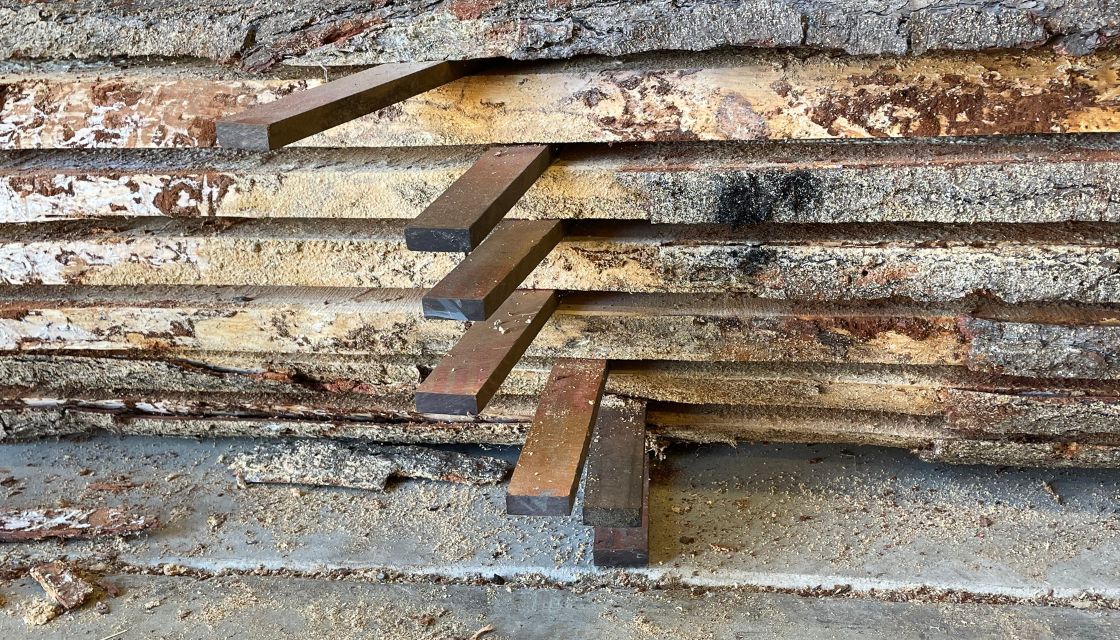
Mayencourt, cross-appointed between the College of Environmental Design and Rausser College of Natural Resources, is prototyping sustainable construction materials and methods in the Wood Lab.
“Forestry thinks about forests up until the point that trees become logs,” says Paul Mayencourt, “and architecture only starts to think about wood after it has been transformed into a building product.” An assistant professor of Cooperative Extension cross-appointed between the Departments of Architecture and Environmental Science, Policy, and Management, Mayencourt dwells in this the gap between the two disciplines, at the nexus of forest management and wood construction.
He describes his approach as “forest to frame,” riffing on California’s famed farm-to-table movement. Most days you can find Mayencourt at the Richmond Field Station, surrounded by piles of logs and scrap wood, lumber in all stages of lamination, and a portable bandsaw. This is where he and Daniel Sanchez, a cooperative extension specialist in ESPM, have revived the former Forest Product Lab as the Wood Lab. In this cross-disciplinary space for hands-on research, Mayencourt and Sanchez are prototyping materials and construction methods that can significantly reduce the carbon footprint of architecture while improving forest health.
DIY mass timber can have a real impact
While some academic research doesn’t make a real-world impact for decades, the Wood Lab is already putting solutions into the field, less than nine months after Mayencourt’s arrival at Berkeley. This aligns with the mission of Cooperative Extension, a 110-year-old program that supports community-engaged research focused on solving environmental problems throughout California.
One of Mayencourt’s primary areas of research is mass timber, a category of engineered wood gaining traction in sustainable construction. These low-carbon, fire-resistant building products offer high strength-to-weight ratios and can be used to create everything from floors and walls to roofs.
“Many people interested in sustainable construction have heard about mass timber,” Mayencourt says, “but they don’t know they can make it in their own backyard with just $500 worth of equipment.”
Using readily available, low-tech tools, Mayencourt is producing code-compliant mass timber products in the lab. He is focusing on nail-laminated and dowel-laminated timber, instead of the more traditional glue-laminated timber or cross-laminated timber. These are easier and faster to deploy in the current conditions in California.
Mayencourt plans to use his lab-made dowel-laminated timber in a structure he is designing for the Oxford Tract Farm in Berkeley. The building will be simple — essentially a roof sheltering an outdoor classroom, storage facility, and washing station — but can serve as a proof of concept for DIY mass timber.
Mayencourt and Sanchez also plan to teach their process of mass timber production at community workshops, transferring knowledge about sustainable construction practices.
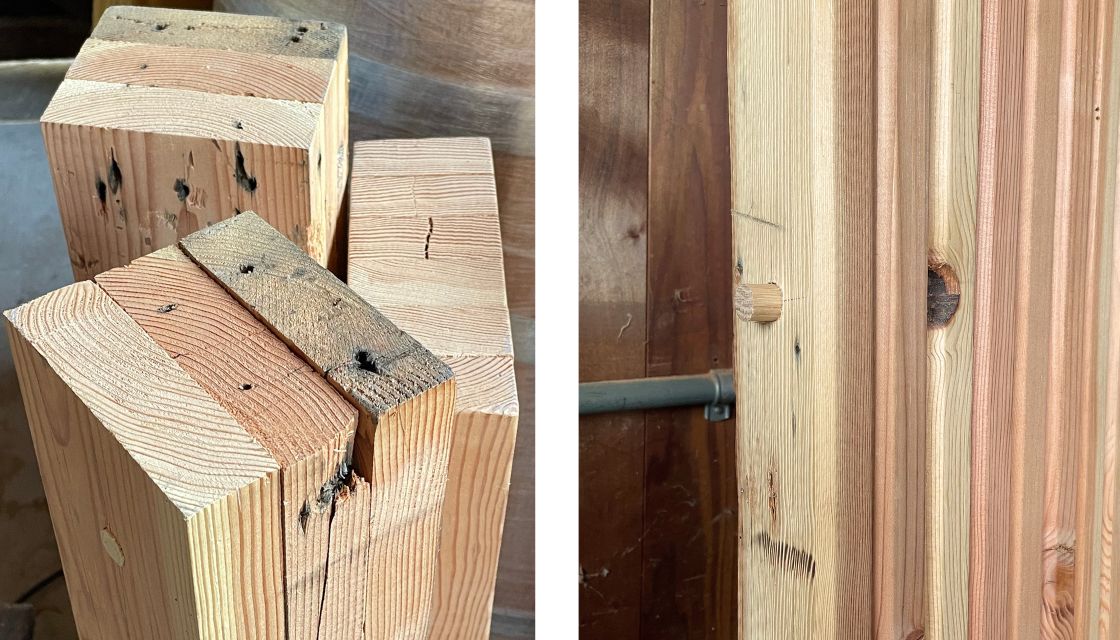
Solar kilns reduce carbon footprint of mass timber production
Mayencourt is also exploring ways to reduce the environmental impact of drying wood, a necessary step in converting logs into usable building material. “Up to 90% of the embodied carbon in lumber is a result of the drying process,” explains Mayencourt.
In a grassy field colonized by Canada geese at the Richmond Field Station, Mayencourt and Sanchez show off the solar kiln they assembled from materials bought at Home Depot. With box fans powered through solar panels and a south-facing angled roof made of clear plastic sheeting, the kiln can dry wood in 30 to 45 days, depending on the weather conditions and the wood species.
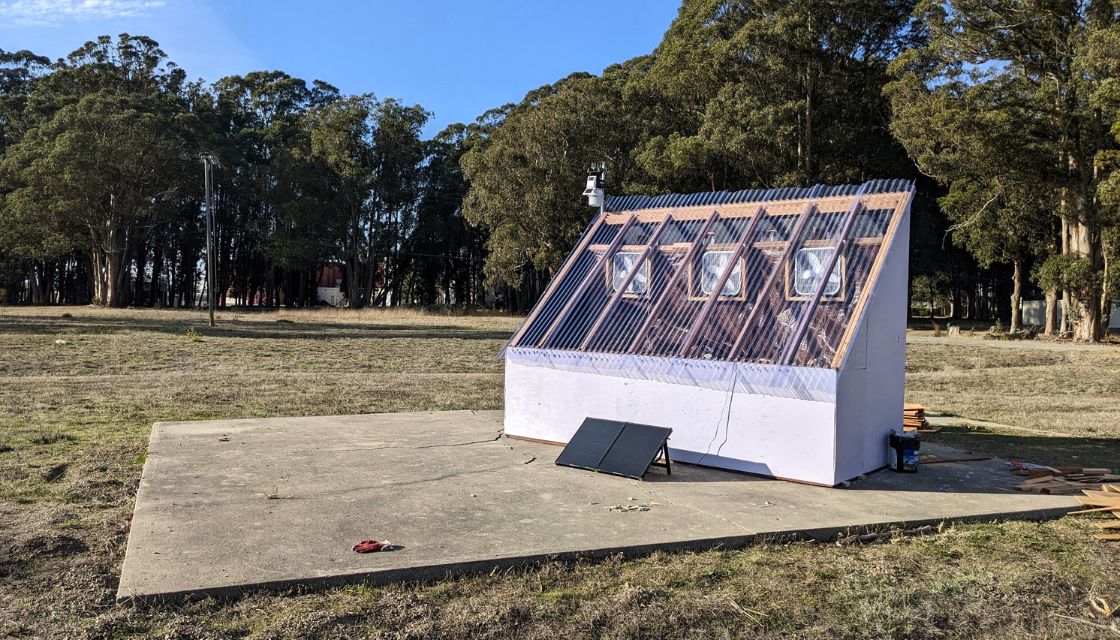
Solar kilns are an essentially free, low-carbon method of removing moisture from wood, in contrast to industrial kilns that rely heavily on large amounts of energy. While not a new technology — Mayencourt notes that the Whole Earth Catalog published instructions for building solar houses in the 1970s — they can play a key role in reducing the amount of energy used in wood construction.
The design built at the Richmond Field Station is inspired by a publication by Virginia Tech Cooperative Extension. “However, we are upgrading this technology with new construction materials, structural geometries, and computational building thermal analysis to increase its performance up to the industrial scale,” says Mayencourt. And like DIY nail- or dowel-laminated mass timber, anyone can make a solar kiln.
Producing mass timber on-site protects forests and reduces carbon footprint of construction
Mayencourt is working to scale up the production of mass timber from the backyard to the lumber yard. Architects and builders in California are beginning to use mass timber more widely, attracted by its low carbon footprint. But despite its extensive forestlands, the state currently relies heavily on imported mass timber.
One of the challenges facing California’s forest management, Mayencourt explains, is that it no longer has the resources to process its lumber into high-added value wood products. Since the 1980s, the capacity of California’s sawmills has been halved, during which time the state’s attention turned to forest preservation, increasing the risk of wildfire.
The idea Mayencourt and Sanchez are proposing is to create a closed-loop system: California can remove small-diameter fire-prone trees from its forests, process them locally into mass timber products using low-tech carbon-neutral equipment like solar kilns and portable saw mills, and use the resulting mass timber for sustainable construction projects nearby.
This approach would not only help prevent wildfires but also create local jobs, while at the same time reducing the state’s reliance on imported building materials. Like the farm-to-table movement, connecting end users with local products eliminates the energy costs of long-distance transportation.
“Challenges in forestry can be seen as opportunities in architecture,” says Mayencourt. He is also investigating how to build sustainably with other timber resources that currently lack a commercial application, including underutilized California hardwoods, recycled lumber, and logs charred by fire. For instance, the Wood Lab is partnering with Urban Machine, an Oakland startup specializing in salvaged lumber processing. Urban Machine has developed a machine that efficiently removes nails and screws from used wood using AI technology, transforming it into a viable resource to be reinserted into construction or production of engineered mass timber products.
Now, the Wood Lab, Urban Machine, and All Bay Lumber are developing a new machine to make dowel-laminated timber panels for small-scale distributed manufacturing, using a mix of salvaged and fresh-cut lumber. Production is planned to start this month.
Recalling September 9, 2020, the eerie day that smoke from the North Complex fires blocked out the sun in the skies above the Bay Area, Mayencourt says, “the goal is to not have more ‘orange days.'”
Read about the history of the Forest Products Lab on the Rausser College of Natural Resources website>